Centriair is exhibited ColdOx Systems at Anuga FoodTec 2022.
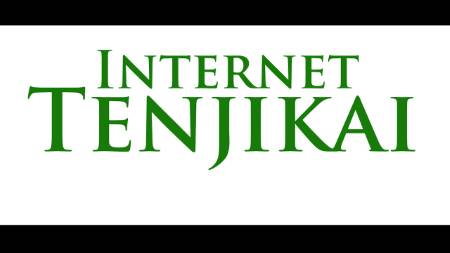
Hi there, we are Centriair, swedish company specializing in order control and particle separation.
We work mainly within the waste biogas and food sector.
We work mainly within the waste biogas and food sector.
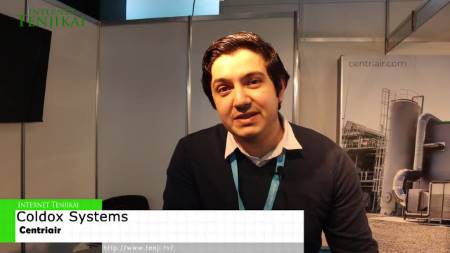
And our technology consists of combining the ultraviolet oxidation techniques, together with a carbon filter which we call ColdOx system.
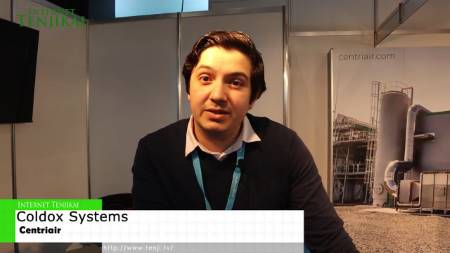
Here you can see the smaller version of the coldOx system which we call coldOx compact.
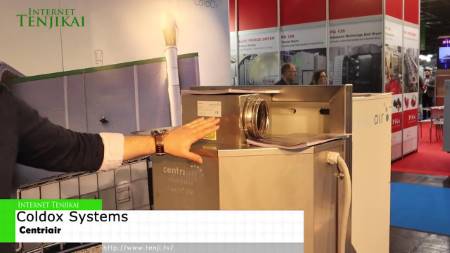
You have the UV lamps inside and the carbon system on the peripheral surface of the unit.
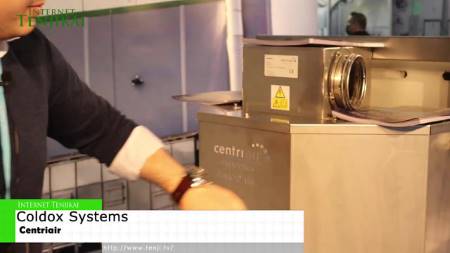
This system is ideal for municipal pumping stations or small waste storage areas that have that have bad smell and cause a lot of trouble for the neighbors.
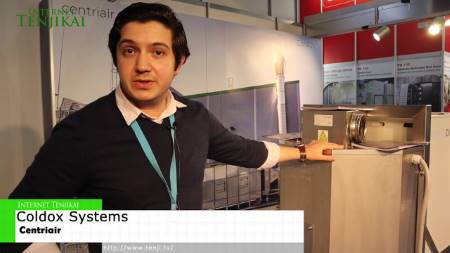
We also have the larger version of that coldOx system right here, this is more of an industrial solution
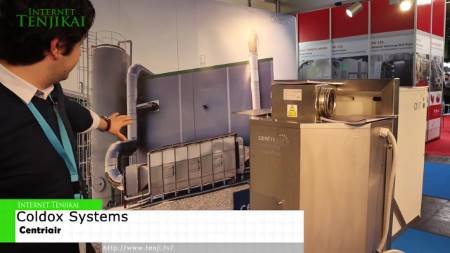
for large waste reception or waste sourcing facility, as well as a biogas processing facilities.
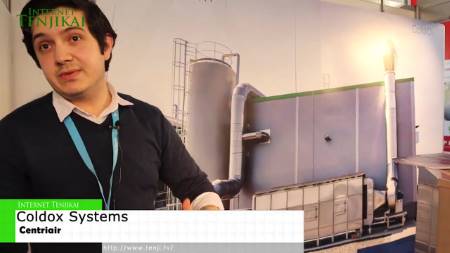
Also in the food sector as well, what happens is you have all your other resources going into one ventilation duct
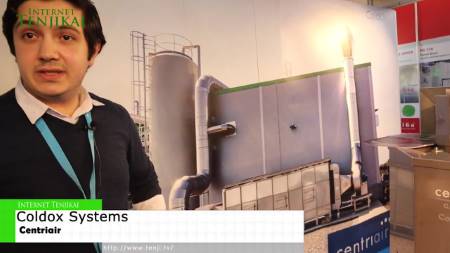
and then that duct is being extracted by our system, the air then goes into our ultraviolet technology where we expose the gas to uv radiation.
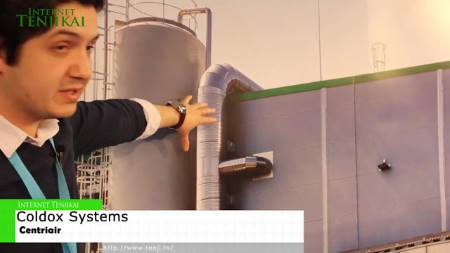
And then followed by an active carbon filter and you can see you can see the full concept here.
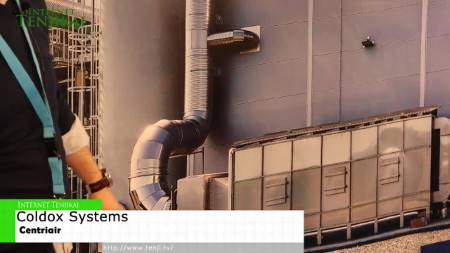
For this project and this is actually a waste bunker extraction where we have achieved 95 order reduction.
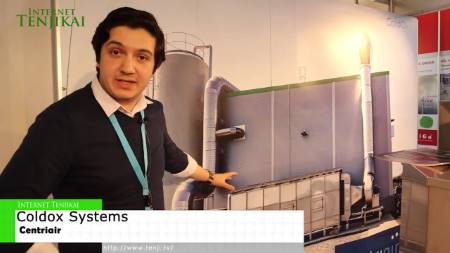
The beauty with this system is that we guarantee at least 95 percent order reduction.
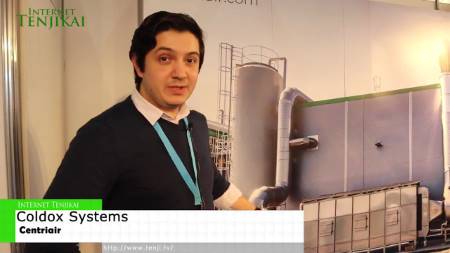
And vocs here we have a different unique type technology which is a catalytic converter.
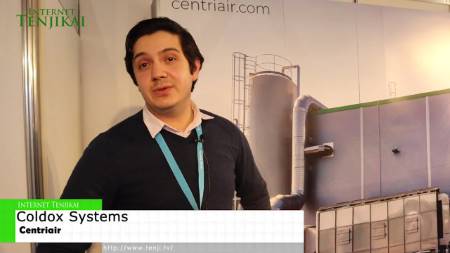
This catalytic converter deals with applications with extreme concentrations.
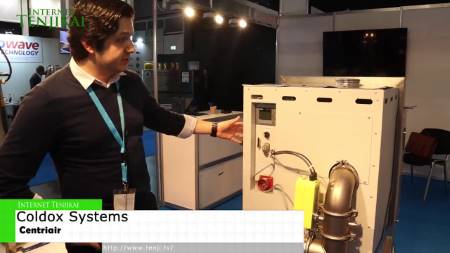
When i say extreme, I mean in millions of other units a good example of this application is that is when you install it for instance at pasteurization tanks, hygienization tanks
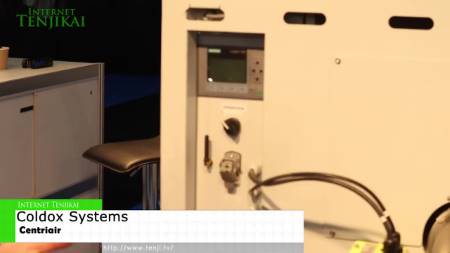
and other storage areas where you have uh really high concentrations of vocs.
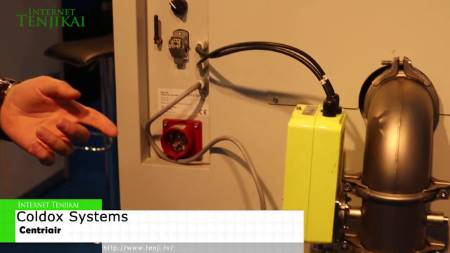
And all doors so what happens is it’s a patented catalyst inside,
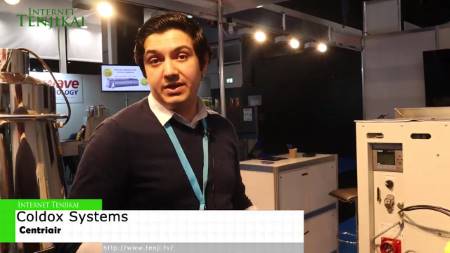
this technology that is heated up using only electricity which makes it quite environmental friendly.
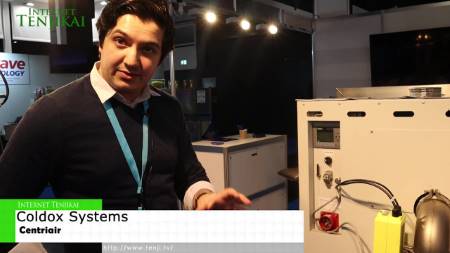
It has its own heat exchanger which means all the heat energy that’s inside the unit is kept in the unit.
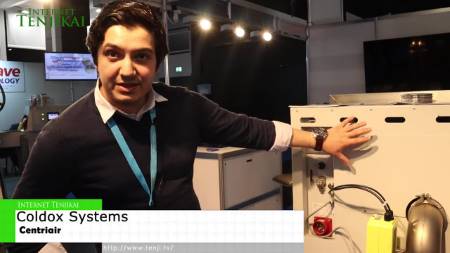
Therefore minimizing the power consumption so the power consumption of a unit then drops down to six watts per cubic meter.
The difference between the inlet temperature and outlet temperature is only 20 degrees.
The difference between the inlet temperature and outlet temperature is only 20 degrees.

which means all the 400 degrees are more or less kept inside this unit.
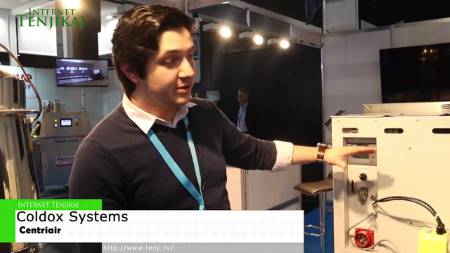
The centrifuge solution is what we offer within the frying sector it is a technology that we use for separating oil particles from the fryer.
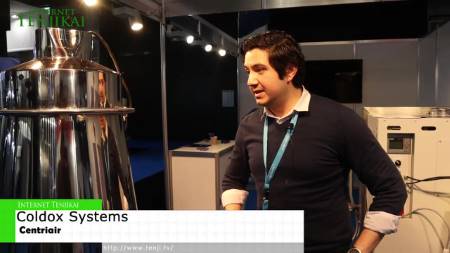
When you fry potatoes chicken meat there is a lot of oil droplets,
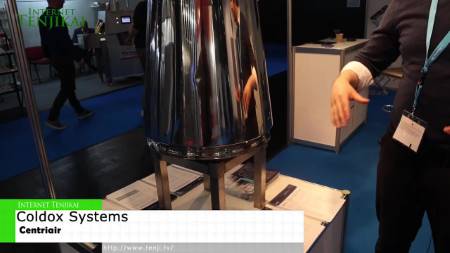
that escape the fryer and enter the ducks mix together with the dust and create first of all a fire hazard.
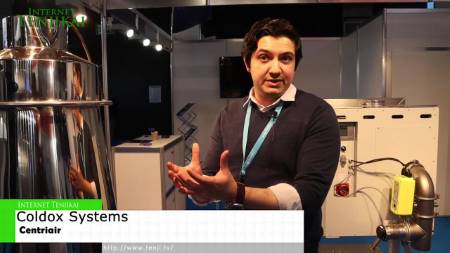
And then also economically it’s quite expensive to keep cleaning those ducts.
So the centrifuge solution allows the customer to capture
So the centrifuge solution allows the customer to capture
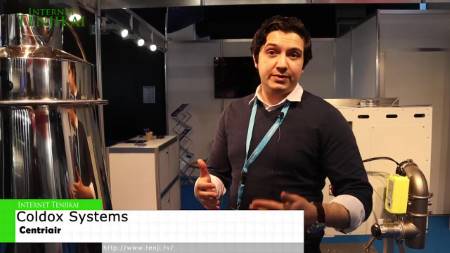
those oil particles from the fryer with a hundred percent efficiency,
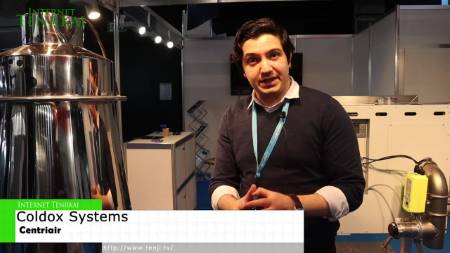
so the centrifuge captures all particles down to the size of one micron making the gas virtually clean after the centrifuge.
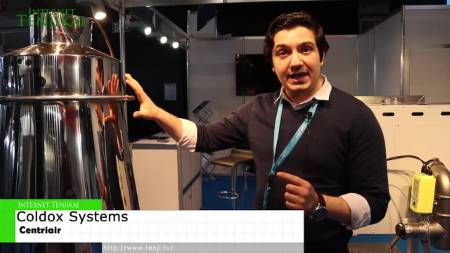
We then combine the centrifuge together with our coal dock system over there.
We get a very good order reduction and particle separation at the same time.
We get a very good order reduction and particle separation at the same time.